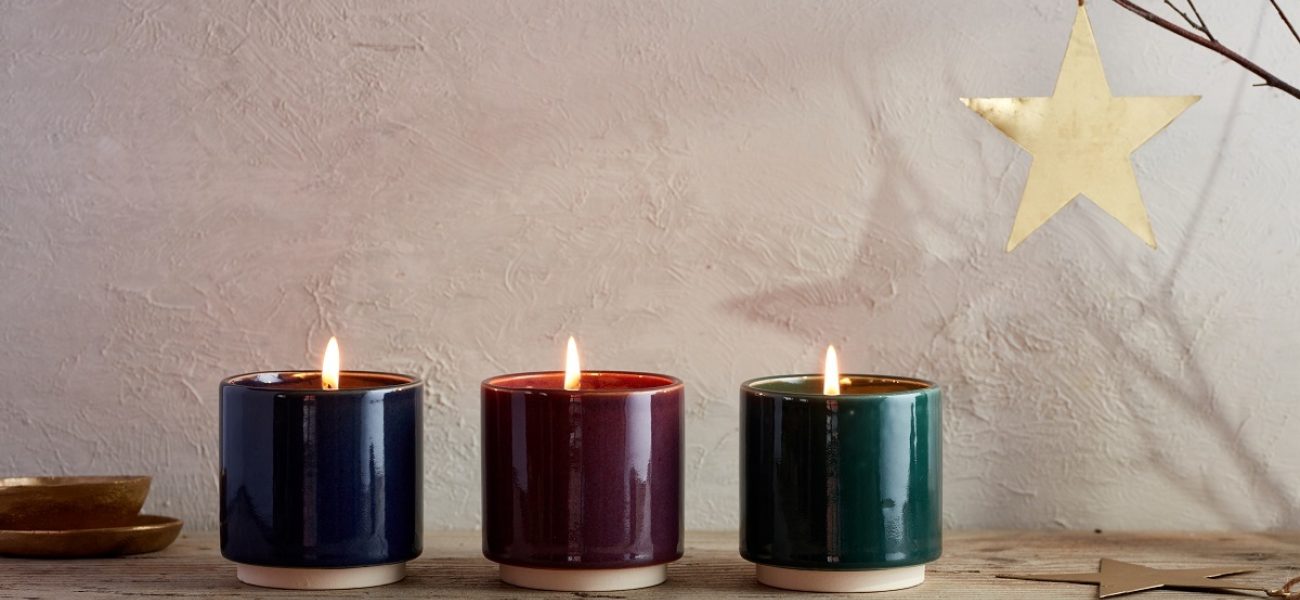
A Leading Light
Candles in some form were invented by all early civilisations to provide light. Originally, they were made of tallow (animal fat) with an embedded wick, using whatever fat was available locally.
Tallow from cattle and sheep was most common in Europe. Candlemakers (known as chandlers) made and sold candles, some going from house to house making candles from kitchen fats saved that purpose. In lands where olives could be grown, oil lamps were an alternative, with the wicks suspended in olive oil. One can only imagine the smell. Indeed the manufacture of candles was banned within some European cities. Beeswax was sought after for its clean burning and pleasant aroma and was the clergy’s choice because its clean burn reduced the soot damage to religious images within church buildings. Medieval clergy also liked the idea that it represented purity because it was made by worker bees which had never mated. Spermaceti, which comes from an organ in the head of a sperm whale was similarly prized but these were only available for richer households. Thankfully spermaceti has not been used since the international whaling ban in 1987.
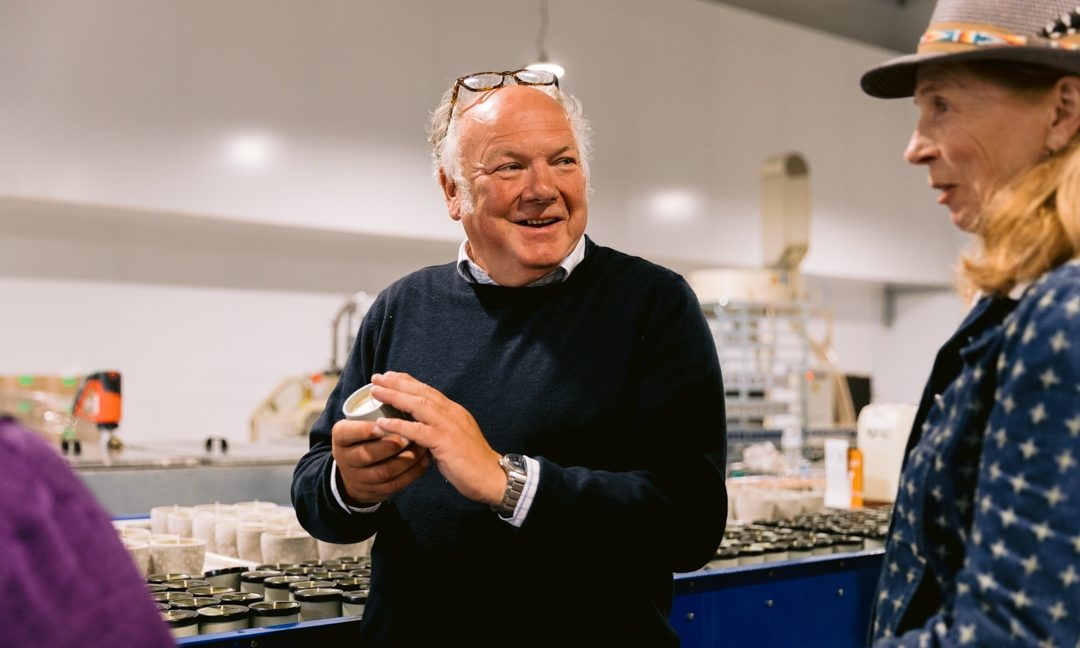
Industrialisation in the 19th century drove the mass production of candles and saw many developments. The introduction of mineral wax (paraffin wax) was a big improvement, but its low melting point caused the candles to distort. The addition of stearin solved this problem and paraffin-stearin blends are in use today to provide clean burning candles with no unpleasant odour. Attention was also given to developing wicks, and instead of using strips of cloth, reeds or rushes, or twisted strands of cotton, candlemakers started using tightly plaited strands. This made the wicks curl as they burn, maintaining a steady height of wick and flame.
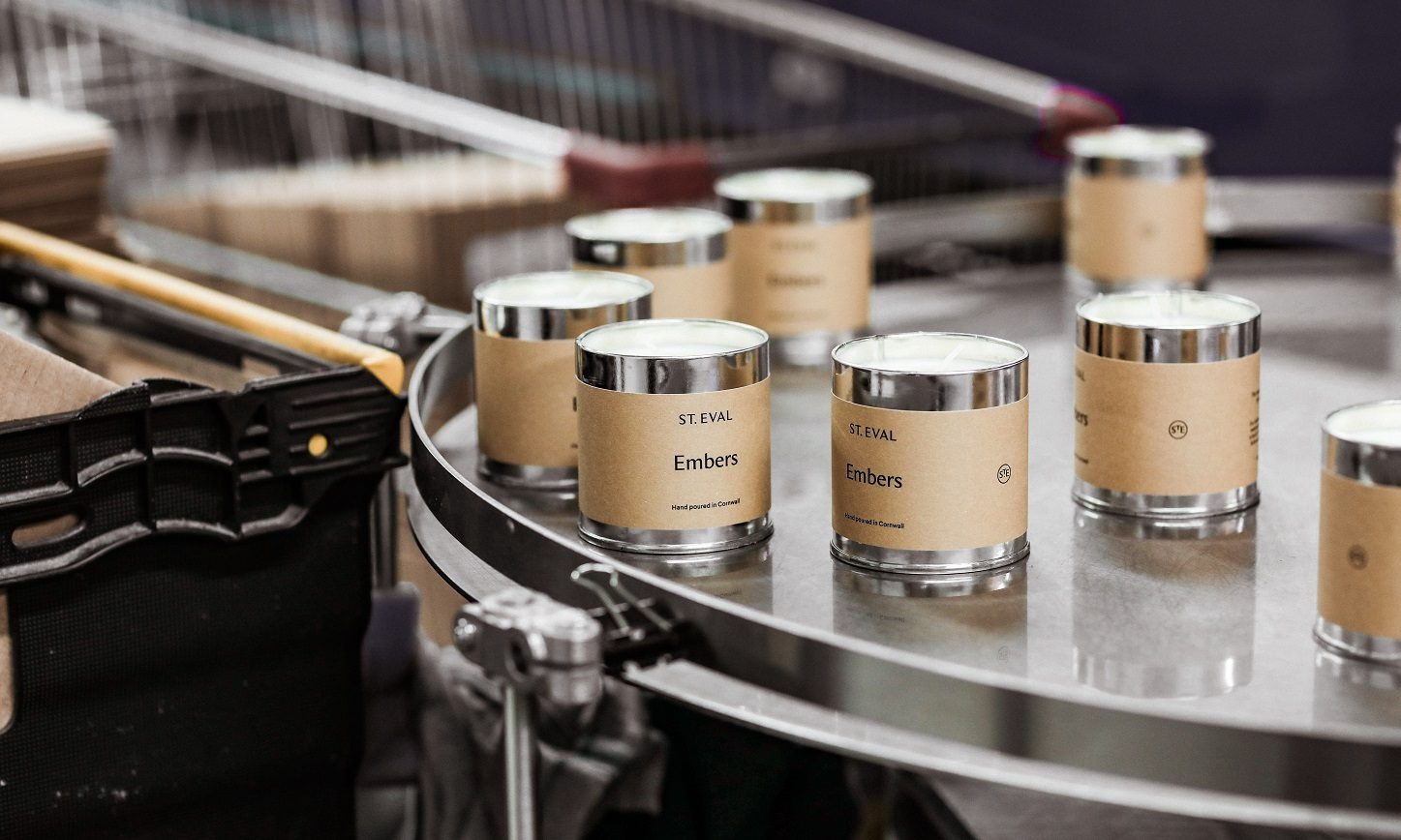
The candles made today by St Eval are sublimely different. The gentle light and delicious fragrance of their candles are pleasures every household can enjoy. But the quiet simplicity of a burning candle belies the effort and care that goes into its production. Each of St Eval’s candles needs a different recipe to achieve the correct balance of wax, fragrance and wick. The smell of the unlit candle (the cold throw) may not be quite the same as the hot throw which fills the room when the candle burns, but both must smell good. The fragrance affects the way the wax burns, the wax affects the way the fragrance is released. The wick is “the engine of the candle”. Each combination of wax and fragrance might require a different wick. Too small a wick gives a weedy pool of melted wax to release the fragrance whilst too big a wick can lead to smoke and soot. The factory keeps around 70 different wicks to select from.
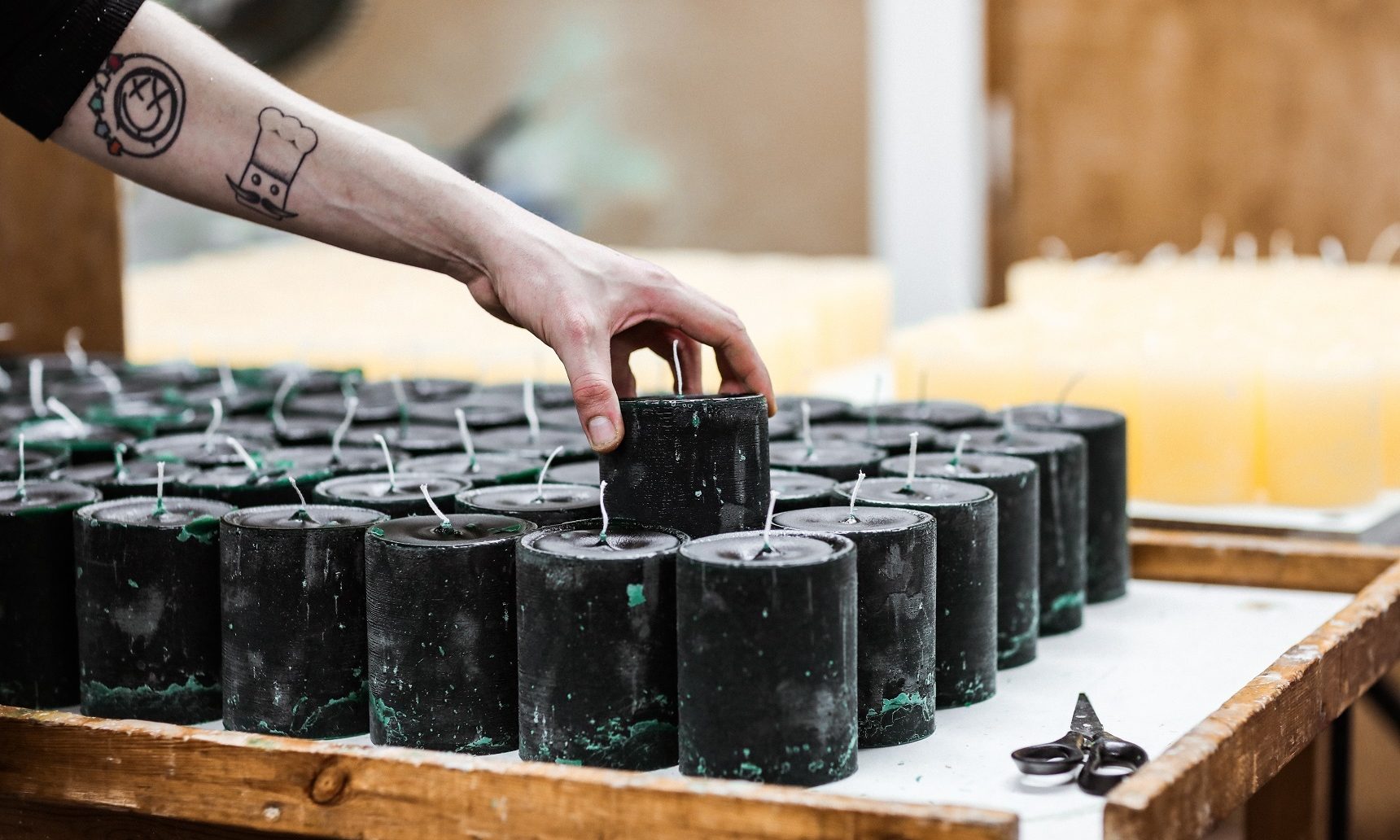
There are important safety aspects to be considered as well. Every component of a candle must be tested for safety, including any colourant, or decorative finish. All St Eval’s candles exceed the legal safety requirements for candles. Their technical expertise in this area has led to a collaboration with Trading Standards who now seek their advice on candle-related matters.
The wax for each candle is a blend of mineral and vegetable waxes, including stearin. The latter adds opacity and helps lock in the fragrance. It is hoped to increase the use of vegetable oils in the future, particularly rapeseed oil as this can be grown locally. For drawing, the technique of making thin cylindrical candles on a continous wick, no vegetable alternative is currently suitable. The fragrances used are mostly blends, citronella and lavender being exceptions. The fragrances are subtle and gentle, inspired by the local landscape and plants. They are largely sourced in the UK, though some come from Grasse, the centre of the French perfume industry. It is easier to get a good throw from floral fragrances whilst the resinous ones, like sandlewood, can be much harder. Provided all goes well, a new candle can be tried, tested and ready for manufacture within several months. Most take longer.
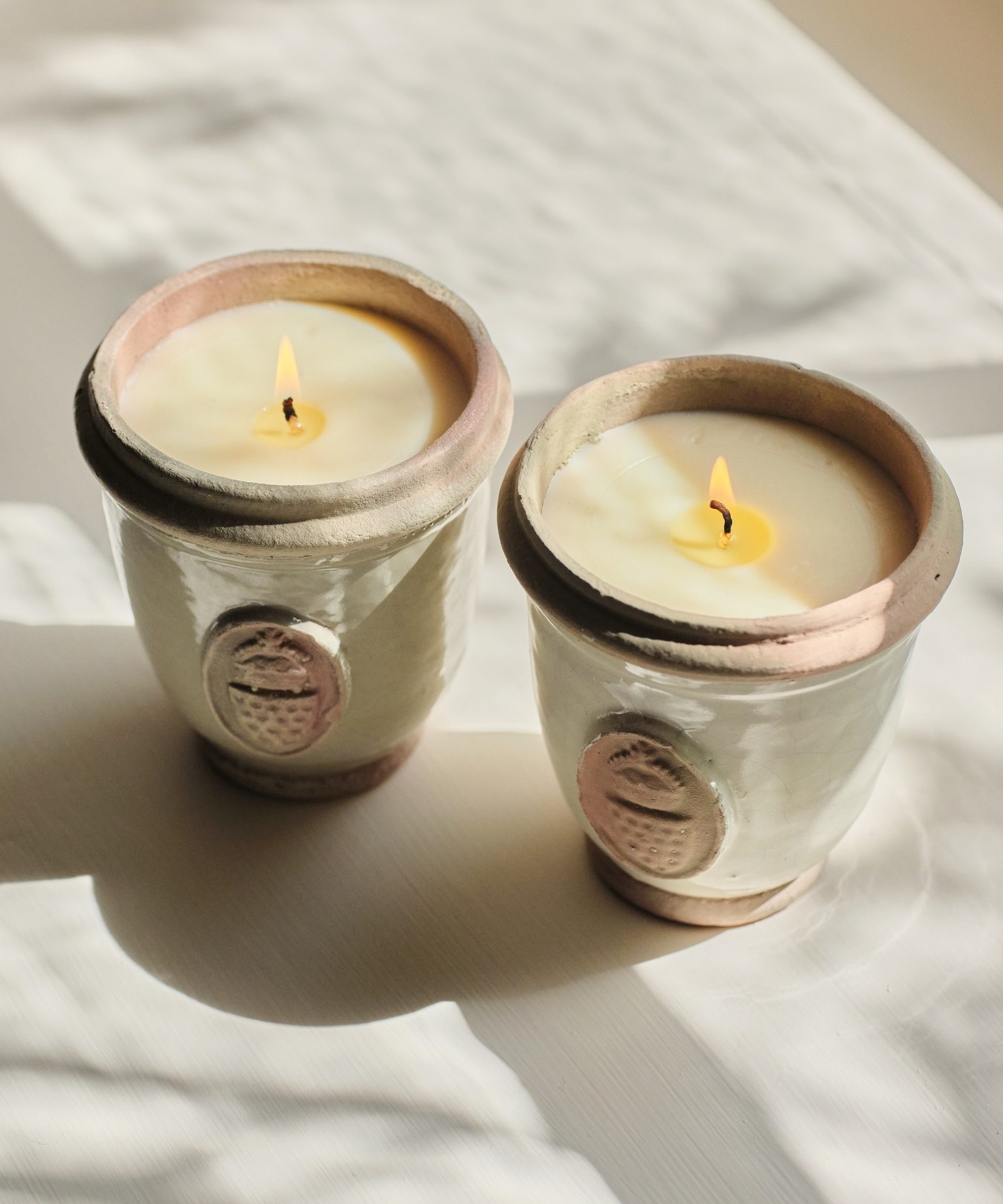